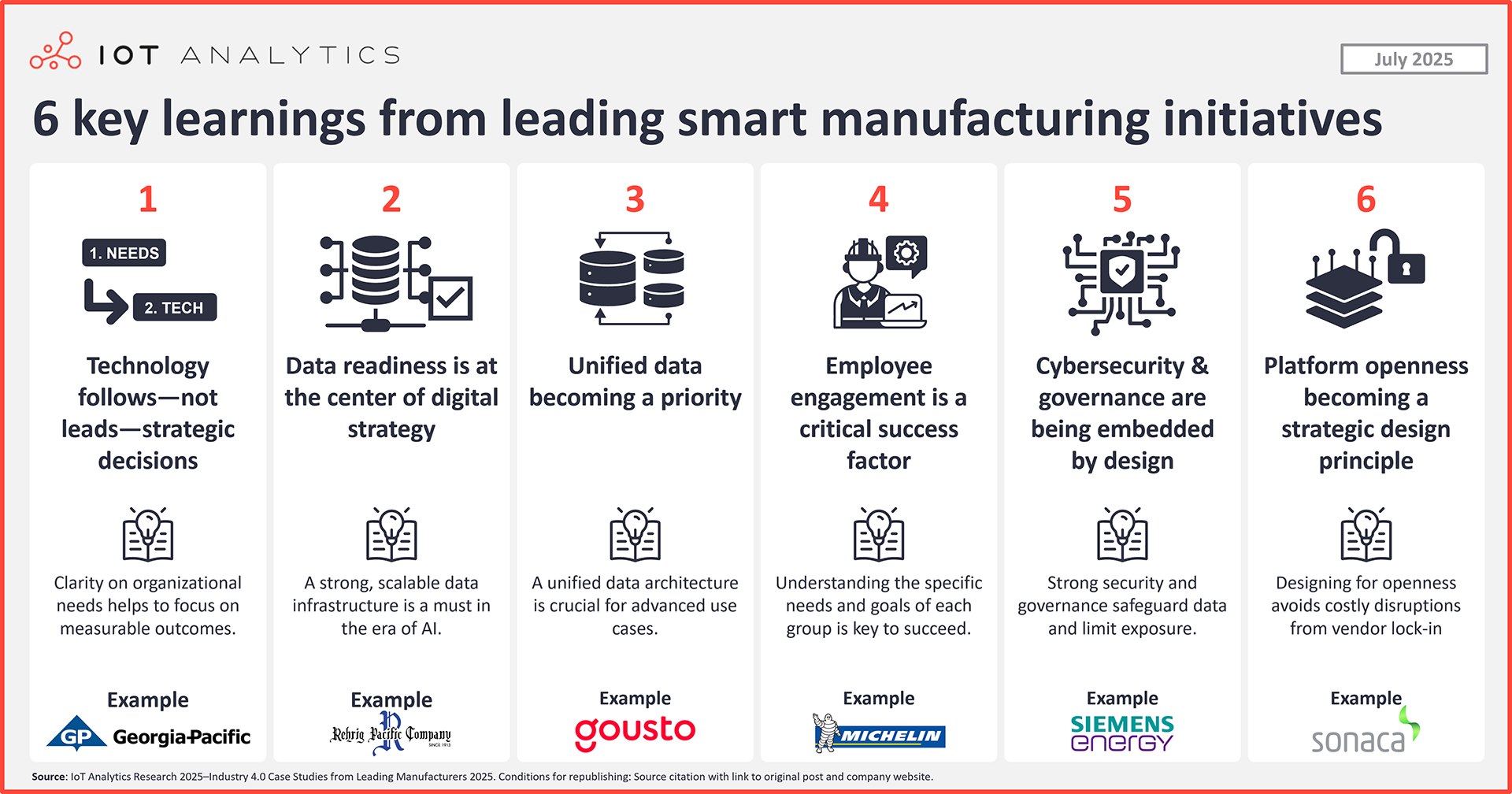
In short
- 6 key learnings stand out from the 2025 IoT Analytics’ Industry 4.0 Case Studies from Leading Manufacturers 2025 report, which delves into 10 recent smart manufacturing case studies from leading, award-winning manufacturers.
- The highlighted manufacturers prioritize operational needs and people before technology, invest in data readiness and scalable architecture, and increasingly stress open interfaces.
Why it matters
- For manufacturers: Understanding why and how industry leaders carry out their digitalization initiatives can help guide operational needs assessments and initiative planning.
- For technology vendors: Case studies are an important source to understand industry digitalization trends to align offerings and go-to-market to help meet manufacturing customers’ needs.
A look behind the scenes of leading smart manufacturing adopters
Every year, as the combined IT and OT market opportunity marches toward surpassing $1 trillion by 2030, the IoT Analytics team reviews and analyzes case studies of smart manufacturing (technology) implementations, seeking insights into how leading manufacturers are currently investing in and carrying out digital transformation initiatives. This year, this research culminated in the 130-page Industry 4.0 Case Studies from Leading Manufacturers 2025 report (published July 2025). After some feedback in the 2023 edition, the 2025 version looks specifically behind the scenes of several companies that have had award-winning initiatives, including those from:
-
World Economic Forum (WEF) Global Lighthouse Network:
- Roche, a Switzerland-based pharmaceutical company
- Midea, a China-based home appliances and HVAC manufacturer
-
Manufacturing Leadership Council Award Winners:
- Boeing, a US-based aviation company, for operational excellence, sustainability, and engineering and production technology leadership
- Ford, a US-based automotive company, for leadership in AI and advanced analytics, enterprise integration technology, and supply chains, just to name a few.
-
Industrie du Futur initiative & awards:
- Michelin, a France-based tire company
Further, the IoT Analytics team chose several case studies for initiatives that, during the research, appeared to be at the forefront of emerging technologies, including:
- Georgia-Pacific, a US-based pulp and paper company, for its AI-based process transformation
- Rehrig Pacific, a US-based plastics and packaging company, for its edge-to-cloud brownfield asset integration
- Siemens Energy, a Germany-based electric company, for its cross-factory platform
- Gousto, a UK-based meal kit delivery company, for its factory data architecture
- Sonaca, a Belgium-based aerospace supplier, for its MOM transformation
In all, the companies—a representative set of the discrete and process manufacturing industries—and their case studies featured in the report are those that the team views as at the forefront of digitalization and, at the same time, openly share major details about their initiatives and advancements.
6 learnings from leading manufacturers
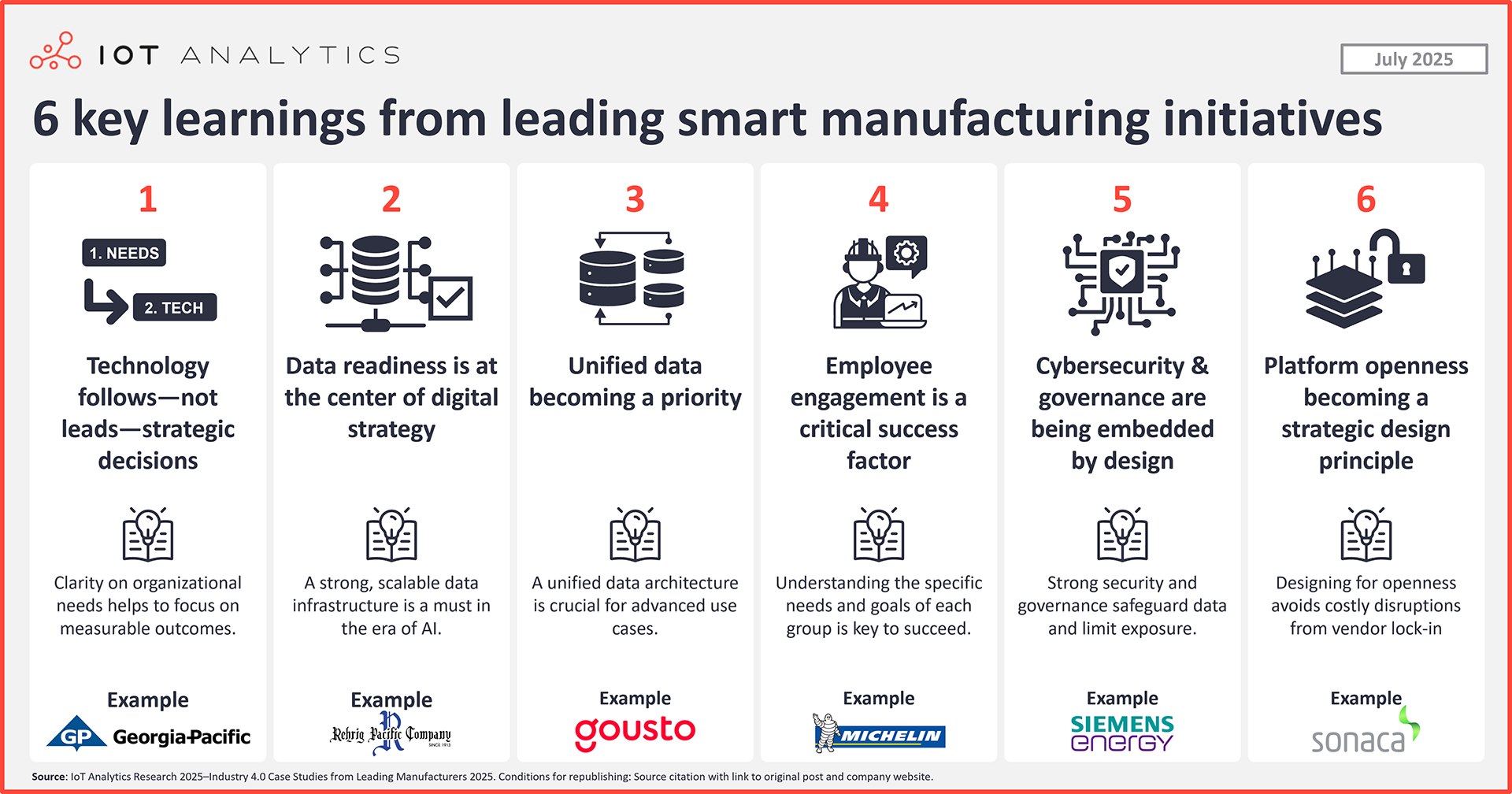
Through its extensive coverage of smart manufacturing topics (e.g., IoT connectivity, industrial IoT, IoT software and platforms, and IT/OT convergence), IoT Analytics is exposed to many past, current, and developing digitalization trends. During its analysis of 10 case studies in the Industry 4.0 Case Studies from Leading Manufacturers 2025 report, the following 6 trends stood out to the team that not only spoke to common themes among the studies but have also appeared in other recent research as well:
- 1. Decision-making: Technology follows—not leads—strategic decisions.
- 2. Data readiness: Data readiness is at the center of digital strategy.
- 3. Data architecture: Creating a unified data foundation is becoming a priority.
- 4. Workforce buy-in: Employee engagement is seen as a critical success factor.
- 5. Security: Cybersecurity and governance are being embedded by design.
- 6. Avoiding vendor lock-in: Platform openness is becoming a strategic design principle.
Insights from this article are derived from
Industry 4.0 Case Studies from Leading Manufacturers 2025
A 130-page report providing an in-depth look at how companies like Ford, Siemens Energy, and Michelin are advancing smart manufacturing in the era of Industrial AI.
Already a subscriber? View your reports here →
Learning 1: Technology follows—not leads—strategic decisions
Clear identification of operational challenges is crucial before selecting specific Industry 4.0 technologies. It appears that CTOs, CDOs, CIOs, and other executives in industrial companies have learned from past mistakes. In past IoT Analytics surveys and reporting (such as the 2020 or 2022 Industry 4.0 Adoption Reports), many executives highlighted that they were too quick to jump on technologies (such as IoT, AR/VR, or even blockchain) and too slow to think through the business case and involve operational teams, noting they would change this approach in the future.
This year’s report shows that leading manufacturers have increasingly come to understand that successful digital transformation projects begin by thoroughly understanding operational pain points, rather than simply adopting new technologies. While advanced tools and solutions can offer considerable benefits, their real value emerges only when they solve specific operational issues identified through direct engagement with the production workforce.
Example: Georgia-Pacific – A practical approach to its top need—knowledge retention
Georgia-Pacific’s approach to digital transformation began with a focus on its operational challenges—specifically, the loss of critical knowledge due to employee turnover. Instead of rushing to adopt the latest technologies, Georgia-Pacific’s leadership took the time to sit down and talk directly with senior factory operators across its facilities in the U.S. This consultation process revealed that the company’s real pain point was knowledge retention, particularly on the production floor, where seasoned workers’ insights were essential for maintaining efficient operations.
“If we don’t ensure continuity of knowledge, one of two things will happen: (1) We lose that knowledge or (2) the knowledge becomes socialized throughout the industry and everybody will be doing the same thing. Either way, we lose our competitive advantage.”
Kurt Adams, (retired) VP R&D at Georgia-Pacific (source)
By listening to frontline workers, Georgia-Pacific identified that the lack of documented expertise in troubleshooting and equipment maintenance, in particular, was worrisome.
With this operational challenge clearly defined, Georgia-Pacific turned to AI-driven solutions to assist with knowledge management and workforce continuity. To build its knowledge base, Georgia-Pacific developed DocGen (short for document generation), a tool that takes recorded interviews with subject matter experts and senior operators, utilizes audio-to-text transcription, and generates properly formatted documents. These documents are then used to train Georgia-Pacific’s generative AI chatbot tool, ChatGP, as well as for standalone training for employees.
Machine operators access ChatGP via a web-based interface to query issues and receive structured troubleshooting guidance, and ChatGP uses retrieval-augmented generation (or RAG) to generate responses based on verified data from DocGen and other documentation. DocGen and ChatGP reportedly aid smoother handovers of critical knowledge between employees and demonstrate how technology, when applied to specific challenges, can drive meaningful operational improvements.
“Using generative AI to pull together information from various sources for quick and easy answers has been a game-changer for us. It’s like having a digital expert who’s always there, ready to help both new and seasoned operators find the right answers fast.”
Ryan Holbird, Senior Manager of Digital Transformation at Georgia-Pacific (source)
Actionable takeaway: Before selecting a technology, manufacturers should conduct thorough operational assessments involving frontline employees. Defining clear, practical objectives can help ensure technology investments deliver tangible, measurable outcomes.
Learning 2: Data readiness is at the center of digital strategy
AI is shifting Industry 4.0 priorities towards data readiness. In the 2023 edition of the Industrial IoT and Industry 4.0 Case Studies report, IoT Analytics noted that several manufacturers emphasized ERP upgrades and cloud migration as the groundwork for digital transformation (e.g., US-based chemical manufacturer Celanese). In 2025, the team did not identify this in the case studies. Instead, a new story has emerged: data architectures and data readiness. This includes not only cloud data platforms but also increasingly edge-based architectures. With growing interest in analytics and even AI, companies are realizing that the real challenge is not just having the right tools, but having the right data, clean, connected, and accessible. This shift brings data architecture to the center of digital strategy.
Example: Rehrig Pacific – Retrofitting the shopfloor for edge-to-cloud data integration
Rehrig Pacific, which operates across multiple manufacturing facilities, faced the challenge of integrating data from a mix of legacy equipment and newer systems. Recognizing that advanced analytics could drive significant operational improvements (most importantly, improving quality and manufacturing flexibility), Rehrig Pacific prioritized building a robust data architecture to enable these tools to function effectively. The company focused on creating a unified data flow from its production floor to the cloud, integrating legacy machines, robots, and different PLCs using a protocol-agnostic edge layer.
To achieve this, Rehrig Pacific worked with AWS IoT SiteWise, US-based industrial automation company Belden’s Horizon DataOps, and Belden’s CloudRAIL gateway to establish an edge-to-cloud data pipeline that centralizes and contextualizes data from its equipment. Additionally, Rehrig implemented a containerized edge architecture that simplified the deployment and scalability of its data solutions. CloudRAIL’s integration enabled Rehrig to connect non-intelligent legacy equipment via bolt-on sensors, allowing for seamless data flow into the cloud-based system.
This infrastructure reportedly enabled real-time analytics across 7 of Rehrig Pacific’s facilities, and the company used the analytics to monitor and optimize the performance of its injection molding machines. For example, predictive maintenance algorithms now analyze vibration data from these machines, identifying potential failures before they occur. In a specific instance, enhanced asset visibility led to a reduction in machine repair time from 4 days to just 2 hours.
“Supervisors once had to check HMIs manually to verify process settings, cycle times, and material mix. Now, dynamic alert thresholds ensure that if no alert appears, everything is correct; if an alert does appear, they know exactly what needs attention.”
Brian Rowe, VP of IT at Rehrig Pacific Company (source)
Actionable takeaway: Having a strong, scalable data infrastructure that extends from the sensor/field instrument level up to the cloud is a prerequisite for developing value-added applications in the era of AI.
Learning 3: Creating a unified data foundation is becoming a priority
A unified data architecture is becoming essential for scalable Industry 4.0 solutions. Manufacturers are increasingly realizing that disparate, siloed data systems cannot effectively support the growing complexity of modern industrial operations. The key to unlocking the full potential of Industry 4.0 initiatives is a unified data foundation that structures and contextualizes data across all operational systems, creating a single source of truth. This enables seamless integration, real-time decision-making, and scalability for future applications, particularly when leveraging advanced technologies like AI and IoT.
Example: Gousto – Creating a unified data platform with FactoryOS
As Gousto was ramping up a new facility, they started facing massive throughput challenges—specifically, costly downtimes. While producing over 200,000 meal boxes a week, Gousto experienced mechanical availability of 70%–85%, which was well below its target and resulted in a massive financial penalty of $30,000 per hour. The company came to realize it could not address the problem because data from its assets was fragmented, it had no clear picture of the state of operations and assets, and its engineering team could only assess the issues once they were addressed.
“[…] we were incurring $30,000 per hour every time we were experiencing downtime. And we didn’t know how to solve it because the reality we were facing was that we didn’t know the state of anything. We couldn’t reason on top of data we didn’t have, and therefore, we couldn’t solve any problem.
Thomas Psaropoulos, Head of Solutions Architecture, Gousto (source)
Gousto set out to bring operational and asset data together, leveraging AWS IoT Core and HighByte’s Intelligence Hub to develop and implement FactoryOS, a centralized platform designed to unify data across its production processes. Built on Unified Namespace (UNS)—a method of organizing and structuring data from various sources into a single, standardized model—FactoryOS integrates factory equipment and key software systems and connects them to a centralized data lake. The 5 key software systems used were:
- Computerized maintenance management system (CMMS)
- SCADA
- Manufacturing execution systems (MES), including in-factory workload routing
- Simulation software and factory twin
- Warehouse execution system
This unified architecture created a single source of truth for all operational data, enabling real-time decision-making, greater visibility, and improved production management. The reported result was an increase in mechanical availability at the site to a consistent 98% and a significant reduction in downtime-related financial losses. By ensuring data is clean, connected, and accessible, Gousto’s unified data infrastructure lays the foundation for real-time analytics, driving long-term operational improvements and enabling future innovation.
Actionable takeaway: Creating a unified data architecture, such as one based on UNS principles, helps ensure that data is consistently structured and accessible. This foundational step is crucial for scalability and can enable more advanced use cases, such as predictive maintenance, AI applications, and real-time decision-making.
Learning 4: Employee engagement is seen as a critical success factor
Digital transformation effectiveness depends on active workforce involvement and buy-in. While technology is a key enabler of Industry 4.0, its successful implementation and sustained value generation are largely determined by how well employees engage with and adopt new systems. Manufacturers must recognize that employee involvement is not an afterthought—it is the core element for realizing the full potential of digital transformation. A well-designed change management strategy that aligns employee needs and objectives with the right technology is important for long-term, tangible business results.
Example: Michelin – Driving energy savings by tailoring software applications to the needs of individual roles
Michelin has implemented an AI-based energy management application across its global manufacturing plants, aiming to optimize energy consumption across the factory floor.
Access Insights+ for $99/month per user
Our Insights+ subscription is an extended version of our blogs that provides additional exclusive insights derived from our reports.
Full report access not included. For enterprise offerings, please contact sales: sales@iot-analytics.com
Disclosure
Companies mentioned in this article—along with their products—are used as examples to showcase market developments. No company paid or received preferential treatment in this article, and it is at the discretion of the analyst to select which examples are used. IoT Analytics makes efforts to vary the companies and products mentioned to help shine attention to the numerous IoT and related technology market players.
It is worth noting that IoT Analytics may have commercial relationships with some companies mentioned in its articles, as some companies license IoT Analytics market research. However, for confidentiality, IoT Analytics cannot disclose individual relationships. Please contact compliance@iot-analytics.com for any questions or concerns on this front.
More information and further reading
Related publications
You may also be interested in the following reports:
- Hannover Messe 2025—the latest Industrial IoT/Industry 4.0 Trends
- Industrial Automation Projects Report and Database 2025
- IoT System Integration and Professional Services Market Report 2024–2030
Related articles
You may also be interested in the following articles:
- Top 10 industrial technology trends—as seen at Hannover Messe 2025
- Mapping 4,000 global industrial automation projects: Where Siemens, Emerson, Rockwell Automation, ABB, and Schneider Electric place emphasis
- The 9 most demanded IoT system integration services
Sign up for our research newsletter and follow us on LinkedIn to stay up-to-date on the latest trends shaping the IoT markets. For complete enterprise IoT coverage with access to all of IoT Analytics’ paid content & reports, including dedicated analyst time, check out the Enterprise subscription.